Ceramic circuit boards are the same as traditional circuit boards, however, instead of the pathways being impressed on metalcore or FR4 baseboards, they are, as the name implies, printed on ceramic ones. If you’re wondering how these PCBs are manufactured, the article below can shed some light on the entire topic. So, without further ado, let’s take a closer look at the list of 4 things that you should know about the process of manufacturing ceramic printed circuit boards:
1. There Are Two Types of Ceramic Printed Circuit Boards
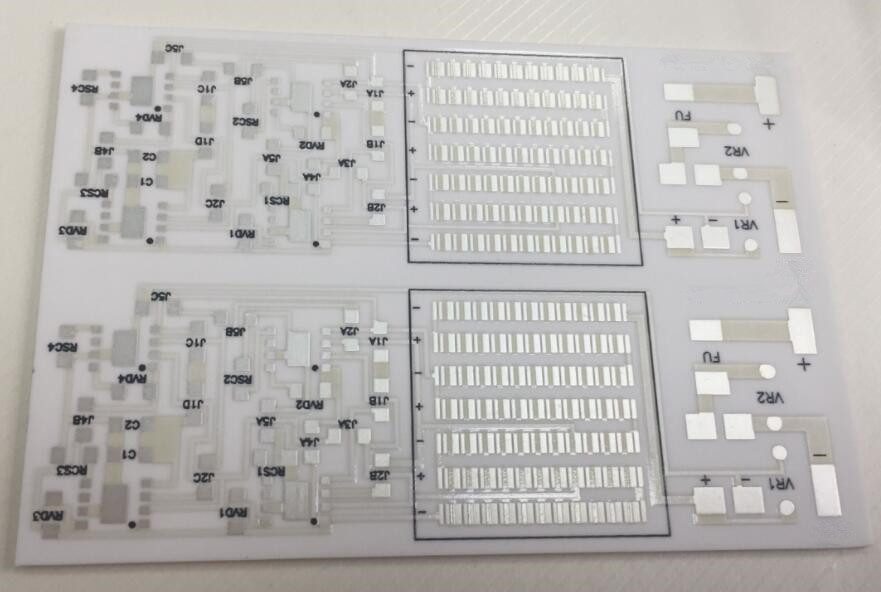
The very first thing that you should know about these ceramic PCBs is that there are two types that you can choose – Alumina and AIN. Alumina, as you might have guessed, is aluminum construction and it most commonly features three layers. The circuit layers are produced from 1 to 10 oz thickness levels and they also have a base that is manufactured from aluminum or copper substrate.
On the other hand, AIN, also referred to as aluminum nitride is a comparatively new material that has been utilized for the last several years, and it’s loved due to its various features, including low thermic expansion coefficient, high conductivity, as well as its good dielectric characteristics. In most situations, they’re employed in microwave device packages, substrates for electrical packages, and of course, molten metal handling parts.
2. There Are Golden or Silver Pastes
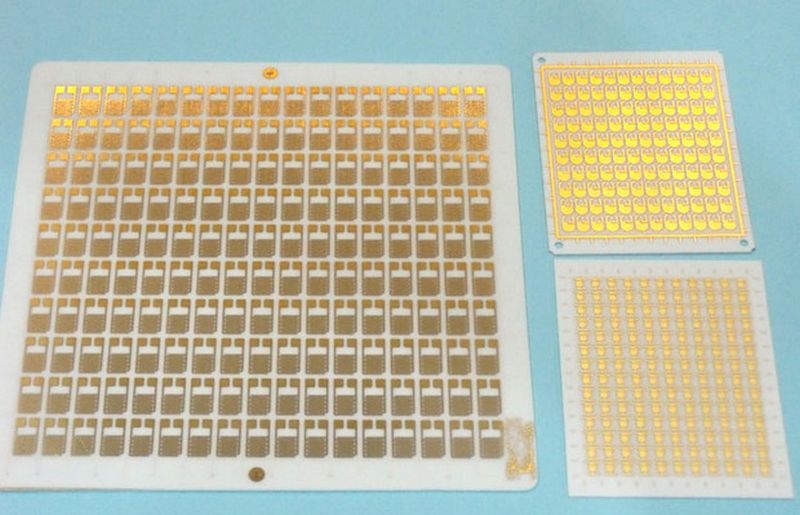
A ceramic PCB could be made with either golden or silver conductive pastes for printing the pathways in every layer. Generally speaking, the metal components or substrate are integrated into every layer with a screen printing process. Additionally, the pathways could be automatically punched in the unburn layer. But, if this isn’t possible, a laser could be utilized to drill the pathways in the ceramic baseboards.
3. The PCBs Need to Be Burnt
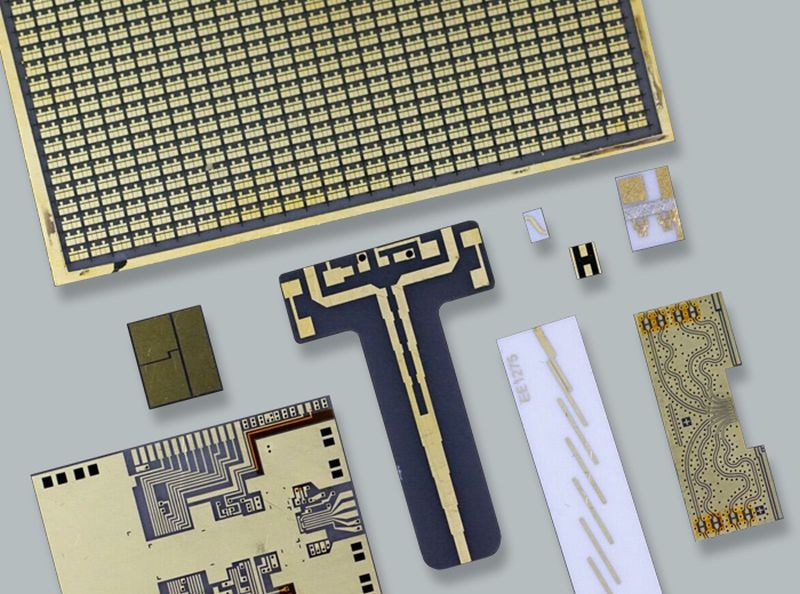
After the panels are piled and printed, the PCB manufacturing company has to be baked in a specialized oven. Almost all manufacturers out there fire temperatures that are below 1.000 degrees Celsius, which equals the melting warmth of either of the aforementioned metals – gold or silver. This means that the lower temperatures are exactly what enables gold and silver to be utilized in the production means of ceramic printed circuit boards.
4. The Thickness Can Go From 0.127 to 2 mm
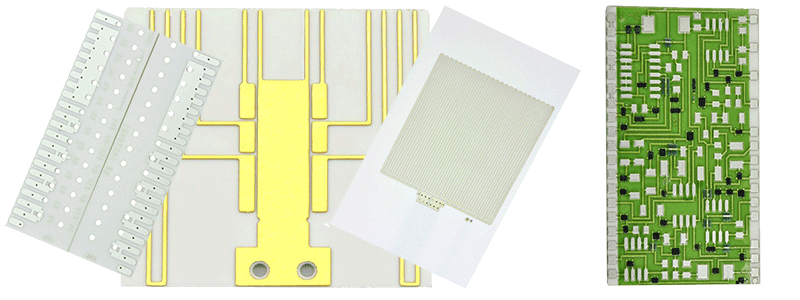
Keep in mind, the thickness of the PCBs can go from 0.127 to 2 mm. However, you should know, it is quite possible to manufacture boards of non-specific standards, which basically means that they can be completely customized. Additionally, besides manufacturing one-sided and double-sided boards, different manufacturers can also be produced in a multilayered form based on raw ceramics, which only allows them to be used for more processes and applications.
Conclusion
Ceramic printed circuit boards are slowly, but surely becoming increasingly popular across various industries, manufacturing, and assembly plants. After all, they offer a wide range of properties, which means that they offer more properties than traditional PCB boards. Hence, if you’re in need of a PCB board that has excellent thermal conductivity and that is very versatile, don’t lose any more of your time. Instead, start looking for a printed circuit board manufacturer that’ll provide you with the services you need.